WHAT DO ADDITIVE TECHNOLOGIES AND JOURNEY TO THE TOP HAVE IN COMMON?
YOU CAREFULLY BUILD LAYER BY LAYER UNTIL YOU REACH A SUCCESS
3D printing is no longer an exotic for a select few! Currently, this is a significantly inflected topic, even in connection with optimization and savings in production or in search of the most productive production method. And your business can move up – a very significant level!
Do you think that additive technology can only offer plastic printing of a prototype? No! In many cases, it can replace mass production, accelerate product development and launch, and help optimize the company’s processes. It even helps people in certain areas.
And I will help you with that!
SEARCHING FOR SYNERGY AND FINDING AN IDEAL CUSTOMER SOLUTION IS A PRIORITY FOR ME. TOGETHER WE WILL FIND SOLUTIONS THAT EXCEED YOUR EXPECTATIONS!
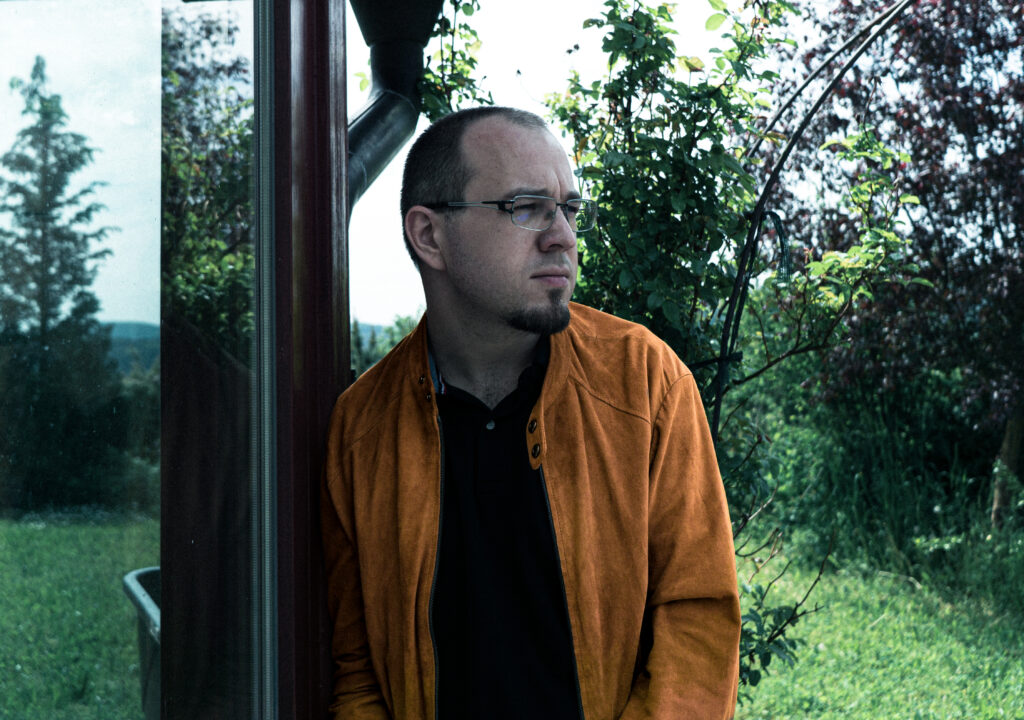
3D Printing
-
Plastic
-
Metal
-
Wax
- FDM (Fused Deposition Modeling)
It is one of the best known and most widely used technologies that use polymeric materials. It uses plastic fiber (so-called filament), which is plasticized in the nozzle and locally layered on the platform. There are many materials to choose from such as ABS, PLA, PET-G, including flexible materials or composite materials for functional parts. Last but not least, there is a serial granulate, which is identical to the material used for the injected parts - it is used in APF (Arburg Plastic Freeforming) technology.
- SLS (Selective Laser Sintering) and MJF (Multi Jet Fusion)
In both cases, the basic principle is sintering the powder (most often polyamide) in the desired location. SLS uses a laser, at MJF we achieve the result with the help of generated heat and a special binder. In addition to functional and visual prototypes, parts produced in this way are also used as parts in production. They take the form of personalized tools and jigs. In some cases, they even replace serial parts! Both technologies are very productive due to many years of development and there is no need to limit yourself to low production.
- SLA (Stereo Lithography) and DLP (Digital Light Proccesing)
For the production of parts, these technologies use a tank with a liquid resin, which is cured by UV radiation. This method of printing is one of the first to be developed for 3D printers and is still widely used today. The laser SLA and the DLP projector illuminate the layer cross-section of the required part. This hardens the polymer. In addition to large-format SLA machines, prototype production also uses MJ (Material Jetting) technology, where instead of a resin tank, the print head material is applied directly to the platforms. Curing occurs using very strong UV lamps on the sides of the print head. Thanks to this, different materials and colors can be combined in the print, without the need for glued joints!
- SLM (Selective Laser Melting) and EBM (Electron Beam Melting)
These technologies use the principle of melting metal powder. In the first case using a laser, in the second using an electron beam. The material is heated to the required temperature at the required point, which connects the individual particles. Unlike SLS, the atmosphere inside the building chamber plays a big role here. A controlled flow of inert gas (argon or nitrogen) is used to stabilize the melting process and a vacuum is maintained in the chamber for the EBM. Since this is a production of a metal part, the subsequent operations required are more similar to conventional production. We need to remove the support structures that are necessary for proper product printing in certain cases (separation from the platform, overhangs, etc.). Removal takes place with a grinding wheel, band saw, etc.
- WAAM (Wire and Arc Additive Manufacturing)
WAAM is a printing method that uses the welding of metal wire in layers and in a protective atmosphere. It is a robot-controlled welding that can be supplemented by conventional machining within a single machine. Thanks to this, it is possible to have a very productive additive machine producing final products in the company!
- FDM
FDM technology is used not only in plastics but also in metals. Instead of plastic fiber, a filament consisting of metal powder and binder can be used. During printing, the binder melts, thus joining the individual layers together. The printed part (so-called green part) is stripped of most of the binder in a special dishwasher and placed in the furnace, where the sintering process takes place, thus creating the final part. The same process uses BJ (Binder Jetting) powder technology, with the difference that the part is created by applying a binder to the powder layers, instead of fiber.
- Wax model printing
It is one of the very strong industries of 3D printing. Models for this method can be produced quickly, accurately and cheaply! It is ideal for piece and small series production. It is used to create a smaller series of metal parts where machining does not make sense. Then comes the casting.
- Lost wax method
A method widely used in both prototype and serial production. Thanks to the technologies used, the wax model is accurate and with fine detail. It can be seen in jewelry, but also in other industries.
Milling
-
Plastic wood
-
Plastics
-
Aluminium
- It has always been associated with development. It is a polyurethane pressed into blocks of different densities and with the addition of various additives (aluminum, polymer, etc.). The individual parts can be joined together before and after machining using adhesives that have the same or better properties than the material itself.
- The method allows the production of unlimited parts. Examples of production from such material are interior and exterior parts of vehicle prototypes, or inspection, measuring or assembly jigs. Plastic wood can also be used for small series forging and pressing tools.
- When 3D printing is not possible, the solution is to produce plastic parts by conventional machining. Thanks to the available semi-finished products, you will receive a part with properties similar to a series-produced variant!
- Machining from non-ferrous alloys, specifically aluminum, is central throughout the industry. It is used for installation parts, functional parts, complex design shapes, jig components and tools. In addition to custom machining of these materials, it is also applicable in other industries.
Casting
-
PU vacuum casting
-
RIM
-
Wax
- Great for large pieces. Where the benefits of 3D printing due to economy, size and machining end, casting comes! The silicone mold exactly copies the smallest detail that appears on each casting. The service life of the mold is 20-80 pieces! The materials are developed to faithfully copy the properties of serial materials. It is a solution for smaller series of functional parts and final products.
- The ideal solution when even polyurethane casting is not enough and an aluminum injection tool is too much of an investment. Reactive injection of two components of the material into flexible molds (silicone as in polyurethanes) or solid molds (plastic wood as in machining) ensures the accuracy and required properties of parts at higher series. In this way, it is possible to produce, for example, bumpers and parts of the instrument panel for cars, various instrument covers, etc.
- By the lost wax casting method, we achieve precise castings in smaller series and from the material you need. It is an ideal solution if you need metal parts and do not want plastics. It will help when machining is not possible either, because you need more parts and the silicone mold cannot withstand the temperature of the molten metal.
- In addition to 3D printing, we can also produce a wax model for this method by casting it in a silicone mold. The result is a precise model ready for casting in a partner foundry. Thanks to this, you get the required casting instead of just a model.
Finishing work
-
Polishing
-
Painting
-
Metalizing
- Parts that require it can be further polished to the required quality. We can finish optical parts for light tests, which have fine optics and special sharp shapes, without any deformation or damage. We completely maintain the accuracy and functionality of the parts! The visible parts are polished into a mirror surface. Imitation plating is created, but with much higher quality.
- We paint parts with classic paints, car paints, metallics and other colors. It always depends on your specific needs. The varnish shapes the final appearance of the part. We therefore rely not only on the highest quality, but also on strict control.
- Vacuum metalizing of parts imitates polished aluminum. The basis is the perfect preparation of the base surface of the part. As a top layer after plating, a clear glossy varnish is applied, which guarantees the basic resistance of the plating.
- Galvanic metalizing pays off from smaller series, when it is economically interesting to create for parts everything that is needed for the realization (holder, jig, etc.). With this type of metalizing, we provide a functional surface without the need for further modifications.
Scanning and CAD
-
3D Scan
-
CAD - data design
-
Reverse engineering
- We can scan parts after production! This will show whether the products are within the required tolerances. It is also normally included in inter-operational controls.
- The advantage of our scanning device is speed and mobility. We can perform scanning directly at your place! After scanning, the data can be further used and a measurement protocol can be created from them according to your requirements.
- Data (2D and 3D) are an integral part of all technologies. The production world cannot do without CAD data. If you don't have data, it's no problem for us! We offer creation of 3D data and their subsequent use.
- CAD - data construction is used, for example, in the production of a part inspection jig. You take the fixture where you place the part and you have an immediate answer if the part is OK / NOK.
- Reverse engineering is a great weapon when you need to transfer a physical object to the digital world and continue to work with it. Do you want to rebuild the old part and make changes to it? Don't have drawings or documents? Does not matter! We can achieve this by combining scanning and CAD.
- We scan the part and create raw 3D data, which we clean and repair as needed. We will make the required changes and we can produce!
About me
Let me go back a few years in time. The history of my enthusiasm for these technologies begins in my 3 years, when, thanks to my father, I fascinatedly watched a laser oscillating on the surface of a liquid polymer. I didn’t understand how this could turn into a solid, functional part.
I also remember the moment when one very expensive printer stopped working. Production stopped. My dad and I disassembled it and put it into operation. It was a challenging task at the time, which we managed together. And wonders could form right in front of my eyes again. Since then, I’ve been happy to return to complex projects. I want to push the boundaries of what technology can do.
Experience
I have been operating in the environment of additive production technology for over 25 years. I have more than 10 years of practical experience with their use. I have been involved in this fascinating production process from the first moment I was given the opportunity. I cut the molds (a few scalpel scars still prove it), ground the master models, cleaned and finished the printed parts. I checked and scanned, created logs. I dealt directly with customers, explained, helped and met their requirements. Last but not least, I delivered the finished parts directly to them.
I KNOW THE INTIRE PROCESS FROM THE BEGINNING TO THE FINAL FORM.
AND I CAN GUIDE YOU THRU IT.
Personal approach
I rely on a sincere and personal approach. I treat every project as an original, because it really is the original. I like to be actively involved and work as a project manager. I always care about customer satisfaction.
THERE IS NOTHING BETTER THAN WHEN I GIVE YOU A PRODUCT THAT IS BETTER THAN YOU EXPECTED!
And if you have any unexpected situation that requires an immediate solution (time lag, production outage), I assure you that I am acting immediately. You can count on me when you give me the information on Friday afternoon. You will have a solution on your desk on Monday morning, or even everything will be resolved. You can have a quiet weekend!
Strong partners
We can find solutions for every project WITHOUT EXCEPTION, also thanks to our strong partners in production and development. They are institutions focused on the development of materials, technologies and also on digitization and Industry 4.0. All this perfectly complements our services. If necessary, we are able to redirect your implementation to the right places.
OUR GOAL IS TO MOVE EVERYTHING FORWARD, LAYER BY LAYER, UP TO YOUR SUCCES AND SATISFACTION
Contact us
Are you interested in the possibilities of using additive production technology? Did you find a method here that could solve your production problem or simplify, speed up or otherwise optimize its process? Not sure, but want advice? Are you simply interested in anything about 3D printing? Feel free to contact us!
Contact us directly
- Vrbický Business Technology s.r.o.
- Jaurisova 515/4, Praha 4